Для получения строительного материала керамзита требуется глина, которая проходит несколько стадий обработки. Особенности технологического процесса заключаются в воздействии на материал резких ударов тепла, позволяющих вспучить сырье, добиться его пористости. Герметизация и придание керамзиту прочности, необходимой во время строительства при воздействии высоких нагрузок, достигается благодаря наличию внешней оболочки.
Подробности изготовления
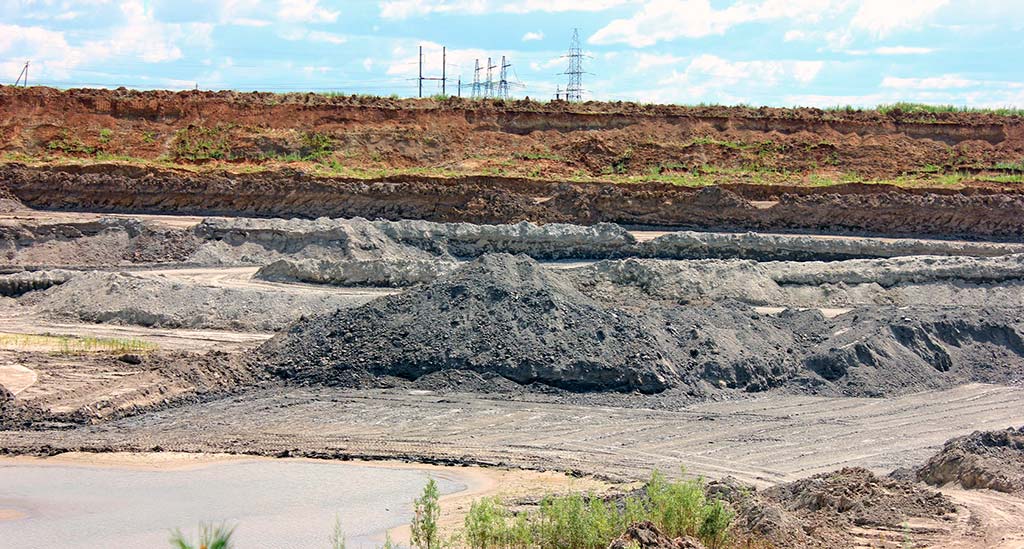
Для получения керамзита чаще всего используются глинистые осадочные породы. Метаморфический тип, например, глинистый сланец или же аргиллит применяется гораздо реже. Сложносоставной продукт содержит в себе также дополнительные минеральные примеси, карбонаты, железо и органику. Наиболее качественный керамзит получается из глины, содержащей не более 30% кварцевых пород. Пригодность ископаемого к дальнейшему производству определяется с помощью таких критериев:
- качество вспучивания во время первичной обработки;
- легкоплавкость;
- требуемые интервалы пористых образований.
Материал не всегда полностью соответствует определенным требованиям, поэтому на производственной стадии нередко искусственно добавляются вещества, способствующие повышению коэффициента вспучивания, такие как железосодержащие элементы, мазут, горные породы и пр. На следующем этапе формируются гранулы, которые требуется просушить, обжечь, а затем охладить. Принцип сортировки материала кроется в свойствах плотности последнего, нередко требуется дополнительное дробление для получений фракций необходимого размера. После всех производственных издержек гранулы фасуются по составу и маркировке сырья.
Стадии и способы производства
Так как главным сырьем для производства керамзита является глина, сначала ее нужно добыть в специальных карьерах для последующей транспортировки к месту обработки. На данном этапе вводятся в эксплуатацию экскаваторы одно- и многоковшовного типа, осуществляющие добычу по всему уровню пласта, а не по частям. В случаях с каменными породами проводятся буровзрывные работы, такая добыча доступна круглый год, в то время как мягкий материал получают только в теплое время года. Непрерывность производства достигается благодаря функциональным объемным хранилищам, где сырье хранится в течение полугода и более. Морозостойкие бункеры предохраняют структуру материала от разрушения, позволяя ему сохранить первозданное качество на длительный срок.

Керамзитовые гранулы можно получить при помощи четырех различных способов, различающихся спецификой и технологиями. От непосредственного качества сырья выбирается один из них:
- пластический;
- порошково-пластический;
- мокрый;
- сухой.
Пластический метод обработки один из наиболее популярных. Сначала рыхлое сырье увлажняется и перерабатывается в глиномешалках или вальцах. Изготовление керамзита сходно с производством кирпича. Конечная масса преобразуется в цилиндрические гранулы на ленточном прессе или дырчатых вальцах, затем продукту придается шарообразная форма. Опционально используются специальные барабаны для просушки или же гранулы направляются сразу во вращающуюся печь. Такой способ характеризуется затратностью процесса, он достаточно требователен к техническому оснащению. Однако именно так производится высококачественный керамзит. В процессе изготовления происходит нарушение естественной структуры глины, что позволяет ее гомогенизировать и значительно повысить коэффициент вспучивания.
Порошково-пластический метод производства подразумевает на начальном этапе полное измельчение материала до порошкообразного состояния. Полученная масса заливается водой и тщательно перемешивается до состояния полной пластичности. Затем с помощью специального оборудования формируются гранулы. Главное преимущество данного способа заключается в возможности создания высококлассного материала идентичного по объемам и размерам, а недостатки кроются в необходимости дополнительного измельчения и просушивания.
Мокрый способ производства характерен для сырья, которое имеет высокий исходный процент влажности. Добытый в карьерах материал помещается в глиноболтушки, где затем смешивается с водой до получения 50-процентного шликера. Сжиженная масса подается с помощью насосов в шламбассейн, а оттуда во вращающуюся печь. После формирования из материала отдельных гранул последние подвергаются сушке на газах, выходящих из печи. Преимущества способа заключаются в возможности добавления присадок во время производства и в очистке используемого сырья от каменистых включений, однако из-за повышенной влажности шликера значительно увеличиваются затраты ресурсов.
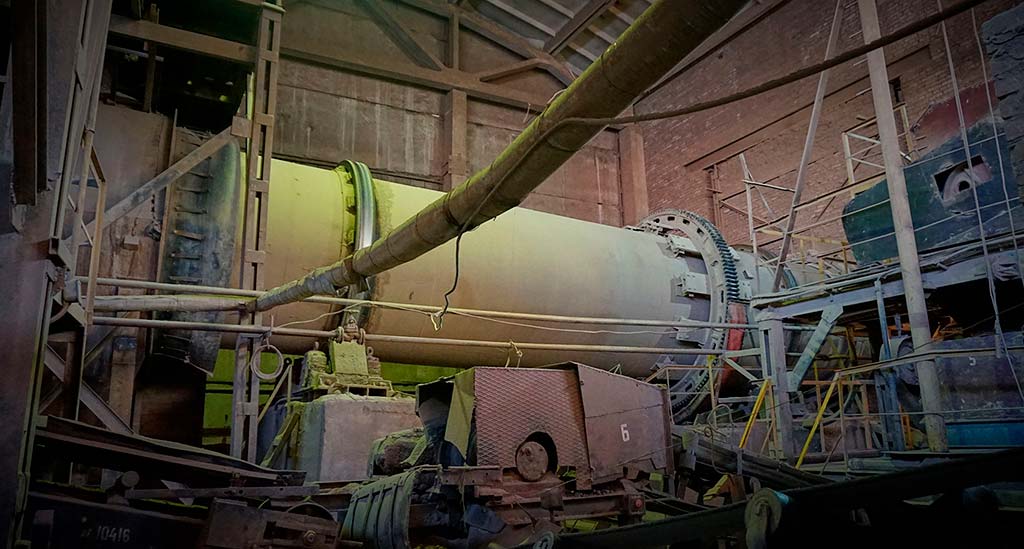
Сухой метод изготовления отличается простотой и применяется при работе с камнеподобными породами. Глина отправляется в дробилку, а потом во вращающуюся печь. Максимальная эффективность сухого производства достигается в случае однородности исходного сырья и изначального отсутствия вредных включений. Его характеризуют низкая энергоемкость и отсутствие внушительных затрат.
Стадия охлаждения
Охлаждение керамзитовых гранул начинается еще во вращающейся печи благодаря поступающим воздушным потокам. Применяются также барабанные холодильники и аэрожелобы. Мобильность обработки определяет свойственную строительному материалу прочность, слишком быстрое охлаждение может привести к появлению трещин, а медленное – к понижению качества путем смятия гранул или их размягчения.
Для получения оптимальных характеристик керамзит должен быть остужен сразу после вспучивания до отметок в 800-900 градусов. После прохождения этапа значения температур опускаются к 600-700 в течение 20 минут. Такой метод постепенного охлаждения избавляет от термических напряжений, образуются кристаллические минералы, характеризующие удельную прочность на конечной стадии. Далее керамзит можно остужать достаточно быстро, после чего в случае надобности происходит фракционирование и дальнейшая транспортировка.
Полная обзор технологии в статье: https://kblok.ru/blog/keramzit